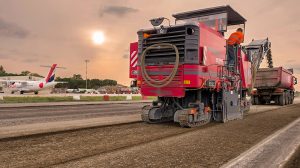
Con más de 6,5 millones de pasajeros (2014), el aeropuerto, inaugurado en 1931, figura entre los siete más importantes de Italia. Los trabajos de saneamiento actuales forman parte de un amplio programa de mantenimiento que tiene como objetivo seguir mejorando la totalidad de la infraestructura. En primer lugar, la atención se centraba en el tramo de la pista de rodaje entre las pistas de conexión TN (Tango November) y TM (Tango Mike); incluyendo el saneamiento del sistema de desagüe, así como el refuerzo de la estructura y la ampliación de los carriles de emergencia: el interior (hacia la plataforma) de 3,50 m actualmente a 9 m y el exterior (hacia la pista de despegue y aterrizaje) de 3,50 a 7,5 m. Las autoridades aeroportuarias también exigieron el asfaltado nuevo y el refuerzo de la estructura de otros 70 m de pista de rodaje en dirección a la pista de conexión TP (Tango Papa).
Además, estaba planeado continuar con el saneamiento del carril de servicio al sur de la plataforma 2, así como, en una segunda etapa, con el saneamiento de la superficie de cuatro zonas de aparcamiento de aviones.
Al seleccionar la máquina, lTea empresa de construcción Bindi S.p.A. confió una vez más en las tecnologías perfeccionadas del Wirtgen Group. La señal de partida la dio, como es usual, una fresadora en frío de Wirtgen, en este caso la W 200 que, entre otras cosas, está predestinada para el fresado selectivo de grandes superficies de capas superiores con altos rendimientos por jornada. En la pista de rodaje de 340 m de longitud, 23 m de anchura y caracterizada por su desgaste elevado, la fresadora grande superó, además, el desafío de fresar la superestructura completa en solo tres pasadas, hasta una totalidad de 70 cm de profundidad. Los encargados se habían visto en la obligación de tomar esta decisión debido a las señales claras de la reducción de la capacidad portante de las capas de base subyacentes.
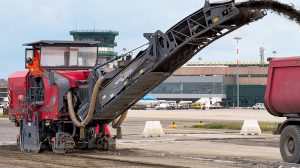
Con el fin de realizar los trabajos de fresado con gran potencia y al mismo tiempo de forma económica, el operador de la máquina hizo uso de una de las numerosas funciones más valiosas de la W 200: las tres velocidades diferentes del tambor de fresado, elegibles a voluntad. Se pueden ajustar cómodamente desde el puesto de mando y, según se requiera, se encargan de ofrecer el rendimiento de fresado ideal. En este caso se necesitaba la velocidad más baja del tambor de fresado. Con esta velocidad y con 558 CV de potencia, la W 200 alcanza el máximo rendimiento de fresado con un bajo consumo de combustible por metro cúbico de material fresado y un desgaste de las picas muy reducido.
La tecnología de reciclaje en frío de las WR 2400 y KMA 220
Sin embargo, antes de que la pista de rodaje pudiera probarse su nuevo traje de asfalto, era obligatorio estabilizar la subbase, que ya no era de suficiente capacidad portante. Una tarea hecha como para las recicladoras y estabilizadoras de suelos de Wirtgen, que otorgan una nueva resistencia a los suelos, añadiendo ligantes, o efectúan el saneamiento de carreteras de forma ecológica, utilizando el material fresado y protegiendo así los recursos; o, por el contrario, ejecutan simultáneamente los dos trabajos de manera fiable, como lo hizo la recicladora y estabilizadora de suelos WR 2400 de Wirtgen in situ.
Puesto que alrededor de un 50% de la subbase estaba compuesta por suelo lodoso y la otra mitad de una mezcla de arena y grava, la recicladora y estabilizadora de suelos la mezcló sucesivamente con cal y en un segundo paso de trabajo con cemento. Después de estabilizar ese suelo de esta manera y hacer que recuperara su capacidad portante permanente, se extendió una capa de 50 cm de material reciclado con un contenido de cemento del 6 %. Con el fin de producir la nueva capa de base, Bindi escogió una combinación de in situ (=en el lugar de las obras) y en planta (=en la instalación), ya que, de acuerdo a las condiciones del lugar, era el método más eficiente. Es por ello que, después de que una excavadora llevara otra vez 25 cm del material fresado originariamente a la vía de fresado, se requería de nuevo el empleo de la recicladora y estabilizadora de suelos de Wirtgen. Esta vez, el potente rotor de fresado y de mezcla de la WR 2400 mezcló el material añadiendo agua y cemento hasta formar una masa homogénea.
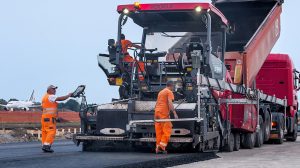
De forma paralela y a solo unos cuantos metros fuera del aeropuerto, la mezcladora móvil de reciclaje en frío KMA 220 de Wirtgen se encargó de mezclar la segunda capa de extendido, también de 25 cm de espesor. Por medio de esta mezcladora, el aglomerado frío se puede producir a partir de las más variadas mezclas nuevas de granos, materiales fresados reciclados y ligantes. Con un rendimiento de mezcla máximo de 220 t/h, la KMA 220 hace posible que cada 6 minutos se produzca una carga completa de camión de 20 t de aglomerado reciclado en frío y se pueda volver a extender de inmediato. En Bolonia, un compactador vibratorio monotambor de 20 t 3520 de Hamm, con articulación de tres puntos y tambor vibratorio liso, se encargó de realizar la compactación final profesional de la capa de material reciclado de 50 cm de espesor.
Finalmente, todo estaba listo para que una extendedora SUPER 1803-3 de Vögele tomara las medidas y se encargara de extender, poco a poco, el nuevo traje de asfalto, compuesto por una capa de base de 10 cm de espesor, 6 cm de capa adhesiva y 4 cm de capa superior. Con el fin de aumentar la vida útil de la capa superior y para que los aviones gocen de una buena adherencia en la nueva pista de rodaje, incluso en condiciones climáticas desfavorables, la capa superior se compone de asfalto mástico de grava, ya que este no solo es más resistente, sino que, gracias a su estructura granular abierta, permite también el fluido óptimo de aguas superficiales.
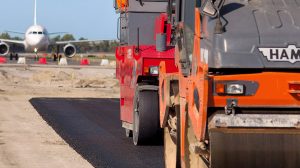
En el caso de la SUPER 1803-3 y con el fin de realizar el extendido de acuerdo al perfil y la posición requeridos, se hizo nuevamente uso del sistema de nivelación automático Niveltronic Plus®, diseñado por los propios ingenieros de la empresa, puesto que, en relación con la facilidad de manejo, la calidad y la fiabilidad, es la solución perfecta para todos los trabajos de nivelación. Niveltronic Plus®, desarrollado de manera óptima de acuerdo con la tecnología de la máquina y basado en referencias preestablecidas, permite alcanzar resultados de extendido de calidad muy elevada y aún mayor al utilizarlo en combinación con el sistema Big-MultiPlex-Ski, como en el caso de Bindi. Al colocar tres sensores de altura ultrasónicos sucesivamente, el Big-MultiPlex-Ski está en condiciones de palpar simultáneamente una referencia en varios puntos distantes entre sí. A partir de estos resultados de medición y con la ayuda del sistema Niveltronic Plus® de Vögele, se puede deducir un nivel de referencia virtual. Especialmente en superficies como la pista de rodaje de 23 metros de anchura, esto constituye una ventaja decisiva, ya que de esta manera es posible reconocer y nivelar fácilmente irregularidades como, por ejemplo, ondulaciones.
Unos compactadores de asfalto de Hamm se encargaron del acabado. También aquí, el contratista de obras Bindi pudo confiar plenamente en las tecnologías líderes del Wirtgen Group. Primero entró en acción el compactador tándem de dirección por traviesa giratoria DV 90, con el probado sistema de gestión de máquina electrónico Hammtronic, que convenció por un gran rendimiento por unidad de superficie y de compactación. Como es usual, un compactador de neumáticos se encargó en seguida del perfeccionamiento final. Los compactadores de neumáticos como el GRW 18 de Hamm juegan un papel importante en la compactación final, puesto que el efecto de amasado de los neumáticos permite sellar la superficie a la perfección. Así como en el caso del aeropuerto Guglielmo Marconi, cuya pista de rodaje ahora está lista de manera óptima para enfrentar las altas cargas dinámicas causadas por el paso de los aviones.
Se cumplieron los estrictos requisitos del proyecto
Elena Sturlini, directora técnica de Bindi S.p.A, también está muy satisfecha con el resultado, ya que los trabajos de saneamiento tuvieron lugar mientras que el aeropuerto estaba en servicio. Esto significó un desafío adicional, además de los requisitos del proyecto que ya eran bastante estrictos, como lo explica Sturlini: «junto a la finalización a tiempo, era sobre todo fundamental asegurar la calidad y la larga vida útil de la obra, con todos los desafíos logísticos que implicaba el proyecto». Es por ello que era aún más importante tener la certeza de disponer de un socio fuerte a su lado. «Sin duda alguna, a través del empleo fiable de las tecnologías del Wirtgen Group, estábamos en condiciones óptimas de cumplir con los parámetros de rendimiento exigidos por las autoridades aeroportuarias, con la más alta productividad posible», aclara la directora técnica.