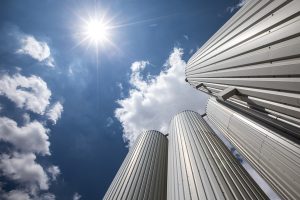
La sostenibilidad ha sido parte de la conversación sobre la construcción de carreteras durante décadas. Sin embargo, las mejoras que hacen que los métodos y las máquinas sean más respetuosos con el medio ambiente siguen ganando impulso.
Los líderes de la industria ven cada vez más las prácticas verdes no solo como una forma de mejorar el mundo, sino también como una táctica para mejorar la rentabilidad.
A la vanguardia de tales esfuerzos sostenibles está el Dr. Hans-Friedrich Peters, Vicepresidente Ejecutivo de la División de Plantas de
Ammann.
El Dr. Peters recientemente proporcionó una mirada en profundidad sobre cómo la producción de asfalto se ha vuelto más sostenible - y un vistazo a lo que está en el horizonte, también.
Las conversaciones sobre la construcción de carreteras "verdes" siempre comienzan con el uso de asfalto reciclado (RAP). ¿Pueden estos materiales reciclados realmente funcionar también como la mezcla hecha de agregado virgen?
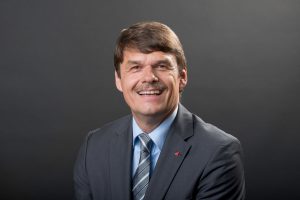
Dr. Hans-Friedrich Peters, Vicepresidente Ejecutivo de la División de Plantas de Ammann.
Sí, la conversación comienza con el RAP - y debería.
Las mayores reducciones en las emisiones indirectas de CO2 resultan de la implementación del RAP.
No deberíamos categorizar el RAP como material de desecho.
Es un sustituto perfecto para los materiales vírgenes. Los agregados en el asfalto recuperado muestran poco envejecimiento y están mecánica y geométricamente dentro de los rangos de calidad del nuevo material.
El betún se mantiene bien, también. Su envejecimiento es limitado y puede ser compensado usando pequeñas cantidades de betún nuevo. Al utilizar el RAP se ahorran tanto los costes de los áridos como los del betún, a la vez que se reducen las emisiones, inicialmente y durante la vida útil de una carretera.
Nuestra tecnología permite el uso de porcentajes de RAP de hasta el 100%. En realidad, el porcentaje suele ser mucho menor en función de la cantidad de RAP disponible y de las recetas definidas por las autoridades.
¿Están los países adoptando cada vez más el reciclaje, o hemos llegado a una especie de meseta? ¿Y qué pasa con los primeros adoptadores - están dando más pasos o se contentan con reciclar a los niveles existentes?
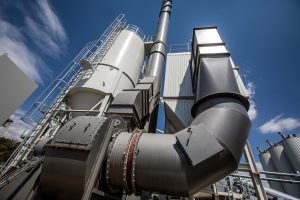
Los gobiernos siguen haciendo más estrictas las normas sobre emisiones.
Muchos países que inicialmente no adoptaron el reciclaje están ahora avanzando bastante rápido.
China es un ejemplo de esto.
El país está aprovechando algunas de las plantas de reciclaje más avanzadas de Ammann y creando una mezcla con porcentajes extremadamente altos de RAP.
Los primeros adoptadores ahora están reciclando aún más. Eso puede ser el resultado de que los gobiernos levanten las restricciones, pero cada vez más se debe a que los productores de asfalto ven el valor del RAP.
Cualesquiera que sean las motivaciones, la comunidad mundial se está beneficiando. Desde una perspectiva ambiental, todas las partes involucradas deben aumentar sus esfuerzos para expandir el porcentaje de RAP que se utiliza para nuevos pavimentos.
El desafío con el RAP es el calentamiento de los materiales. Las temperaturas calientes dañan el betún. En algunos procesos, se calienta el agregado virgen, que se mezcla con el RAP para elevar su temperatura. Pero cuando se hace la mezcla con el 100% de RAP, no hay ningún agregado virgen - y por lo tanto no hay ninguna fuente de calor secundaria. ¿Cómo calientan las plantas de Ammann la mezcla de 100% RAP sin dañar el betún?
En el extremo superior de la utilización del RAP está
la planta de mezcla de asfalto Ammann ABP HRT (High Recycling Technology). Como se ha dicho, puede producir mezcla con hasta un 100% de RAP. No se requiere ningún agregado virgen.
Hay una considerable tecnología e innovación en el concepto de HRT, en particular la tecnología del proceso de secado a contracorriente RAH100. Esencial para el RAH100 es su suave proceso de calentamiento. Durante el proceso de mezcla en caliente, el secador calienta los materiales entre temperaturas de 100ºC y 130ºC. También hace asfalto a 140ºC a 160ºC si se desea una mezcla más tradicional.
El calentamiento es generalmente donde surgen las complicaciones con el material RAP. El RAP debe alcanzar su temperatura objetivo, pero el valioso betún se dañará si el material se calienta demasiado rápido.
El RAH100 elimina esa preocupación. Consiste en dos secciones conectadas. Una es un generador de gas caliente que contiene un quemador y fuerza el aire hacia la segunda sección, que es un secador a contracorriente.
El RAP entra en el extremo más alejado de la sección del secador a contracorriente y se mueve hacia la cámara de calor. Al final del secador contraflujo, el RAP es transportado a un silo que lo acompaña. La mezcla calentada de RAP sale del secador antes de que la temperatura sea excesiva, de modo que nunca alcanza la temperatura crítica en la que el betún se daña.
Un punto rápido sobre el HRT de ABP: Es una planta extremadamente avanzada - yo diría que es claramente el líder de la industria. Sin embargo, Ammann siempre se esfuerza por seguir mejorando, por lo que este sistema, creado hace más de una década, se mejora constantemente. Eso incluye el generador de gas caliente, que ha sido mejorado en múltiples ocasiones.
La apariencia del ABP HRT es única, con el sistema de reciclaje colocado encima del mezclador. ¿Cuál es el propósito de ese diseño?
La planta está diseñada en torno a la incorporación de grandes porcentajes de RAP. Lo que se ve es un guiño al hecho de que la planta de HRT ha elevado el RAP de un papel de apoyo al actor principal.
Como has dicho, la diferencia más sorprendente es que todo el sistema de reciclaje de HRT de ABP está dispuesto verticalmente, en línea directa por encima de la mezcladora. Esto permite que los materiales caigan en lugar de ser transportados, lo que minimiza el desgaste y optimiza el transporte del RAP caliente. El enfoque del HRT también significa que hay suficiente espacio en la torre de la planta para los componentes de alimentación de los aditivos y para llevar a cabo las tareas de inspección y mantenimiento.
Hoy en día el concepto de HRT es el método operacional más inteligente para manejar las propiedades específicas del RAP.
Hacer una mezcla que teóricamente consiste en un 100% de RAP es impresionante. Sin embargo, muchos fabricantes de mezclas utilizan cantidades menores de RAP. ¿Cuáles son las soluciones para estos clientes?
Muchos de nuestros clientes entran en esta categoría, y con toda seguridad tenemos productos para ellos.
Hay varios procesos de calentamiento que dependen de la cantidad de materiales reciclables. El RAH60 es un secador de flujo paralelo donde se puede alimentar hasta un 60% de materiales reciclados en caliente. El RAH50 es un secador de anillo medio que incorpora hasta un 40% de materiales reciclados en caliente.
El reciclaje puede ocurrir en las plantas de Ammann sin estos secadores específicos. Hasta el 30% de los materiales reciclados en frío pueden ir directamente al mezclador, lo que significa que casi todas las plantas de Ammann son capaces de utilizar esa cantidad de RAP.
En algún momento, parecería que los fabricantes como Ammann sólo podían hacer un progreso mucho mayor en cuanto a las emisiones. ¿Hay oportunidades para mayores reducciones?
Las hay. La más reciente es en lo que respecta a los compuestos orgánicos volátiles (COV). Estos compuestos deben ser disminuidos en la corriente de gas limpio para reducir el valor total de carbono
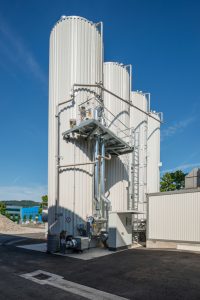
Trabajamos continuamente para reducir las emisiones de CO₂. Esto puede lograrse enfriando activamente el tambor, aumentando la eficiencia del secado y utilizando fuentes de energía como los biocombustibles y el polvo de madera. La tecnología de Ammann puede disminuir CO₂ entre un 10% o incluso considerablemente más, dependiendo de la edad de la planta y la tecnología elegida.
Hay otras oportunidades algo ocultas para reducir las emisiones de CO2, incluyendo el parque de tanques de betún. Una granja tradicional consiste en tanques horizontales calentados con aceite térmico. El cambio a un parque de tanques verticales calentados eléctricamente resulta en ventajas considerables. No hay consumo de petróleo y por lo tanto no hay emisiones. La calefacción eléctrica también es rentable. De hecho, los tanques de betún calentados eléctricamente se han convertido en un estándar en toda Europa y en otras partes del mundo.
También hay otras emisiones como el polvo y el olor. Su nivel de importancia y los valores máximos permitidos difieren enormemente de un país a otro y de una zona a otra. Nuestra tecnología permite los valores más bajos para todos ellos (por ejemplo, < 10mg/m³ de polvo) sin causar ninguna restricción en las operaciones de la planta.
El asfalto de baja temperatura (LTA) es otra oportunidad que se está haciendo más frecuente. Mientras que el asfalto convencional se produce a unos 170°C, los procesos de baja temperatura de hoy en día permiten temperaturas de producción de unos 100°C. Bajar la temperatura de fabricación alivia las necesidades energéticas y, por lo tanto, también las emisiones.
El ALC impacta en todo el proceso de producción, incluyendo el secado, las secuencias de mezcla y el reciclado. Ammann ha centrado nuestra investigación y desarrollo en el proceso completo de fabricación de LTA.
La colocación de plantas en zonas residenciales y comerciales también plantea problemas de ruido. ¿Por qué se ubican las plantas en estas áreas, y qué se puede hacer para limitar el ruido?
La escasez de suelo industrial significa que las plantas de asfalto deben ubicarse cada vez más cerca de las zonas residenciales. Los gobiernos locales pueden tener normas muy estrictas en lo que se refiere al ruido, por lo que tenemos que hacer que las plantas sean lo más silenciosas posible.
Ammann ha sido muy proactivo en este frente. Ofrecemos varios paquetes de supresión de sonido para satisfacer las necesidades específicas de nuestros clientes. Algunos clientes necesitan bajar un poco el sonido, mientras que otros tienen que tomar medidas más sustanciales. Los esfuerzos comienzan con el equipamiento de los quemadores con motores de velocidad variable, que son mucho más silenciosos, y con silenciadores de chimenea, que controlan el ruido del escape. Ofrecemos cada vez más opciones de supresión de sonido, hasta revestir toda la planta.
Ese revestimiento, por cierto, hace que las plantas parezcan edificios comerciales. Son instalaciones hermosas que encajan muy bien en los parques de oficinas urbanos. Los transeúntes nunca adivinarían que hay una planta de mezcla de asfalto en el interior.
Usted se refirió a las emisiones de polvo antes. Esto se está convirtiendo en un problema mayor, ya que las plantas a menudo deben estar ubicadas en zonas sensibles. ¿Se puede hacer algo más para limitar el polvo que resulta de estas plantas?
La conversación sobre las emisiones de polvo comienza con el filtro de mangas. Las plantas de mezcla de asfalto de Ammán eliminan el polvo a través de un filtro de mangas de alta eficiencia. De hecho, reduce el polvo de escape a menos de 10 mg/m3, lo cual es un punto de referencia ejemplar. Actualmente estamos trabajando para reducir significativamente este valor a < 5 mg/m3
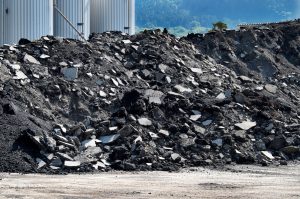
Las mayores reducciones de las emisiones indirectas de CO2 son resultado de la aplicación del RAP.
La gente a menudo se centra únicamente en el polvo resultante del proceso de mezcla, y lo que sale de la chimenea. Olvidan que todas las operaciones logísticas alrededor de una planta de mezclado de asfalto, y alrededor de equipos como camiones y cargadores de ruedas, están creando mucho más polvo que la propia planta. Afortunadamente, países como China, y también algunas áreas de Europa, están considerando cada vez más estas otras fuentes.
Ammann y nuestros clientes han desarrollado juntos soluciones para limitar aún más el polvo. Nos centramos en los puntos de reducción de polvo para mejorar aún más. La toma de medidas en el alimentador en frío, la carga, la campana de salto, el silo de desbordamiento, el área de carga del relleno, la criba, las cintas y los puntos de transferencia marcan una gran diferencia. Eso es además de los esfuerzos proporcionados a través del filtro de mangas.
Para resumir el estado actual de las emisiones, diría que el enfoque principal es recortar el CO2, los COV y los NOx en el proceso de combustión y reducir el contenido de polvo residual después del filtro de mangas. También hay mercados en los que, por ejemplo, se está promoviendo la integración de la predosificación en el proceso de desempolvado.
¿Se están haciendo más estrictos los requisitos de los gobiernos locales en general? Discutimos las emisiones de CO2, sonido y polvo, pero ¿qué pasa con el olor, sobre todo teniendo en cuenta que las plantas están cada vez más ubicadas en zonas residenciales o comerciales?
En general sí, los requisitos se están volviendo más estrictos - pero son extremadamente diferentes de un país a otro.
Estamos ansiosos por cumplir con todos los reglamentos porque es la ley y porque queremos ser buenos vecinos, también. Eso significa mucho más que reducir las emisiones de carbono y COV. También incluye la amortiguación del sonido, que acabamos de discutir, así como el polvo y el olor.
En cuanto al olor... Los vapores de betún son la principal fuente de olor. Ammann ofrece diferentes soluciones para contener los humos y el olor que pueden resultar. Al igual que con el polvo, tenemos puntos de reducción - en este caso los tanques de betún, los niveles de salto y carga y la chimenea.
Se habla mucho de fuentes de energía alternativas, incluyendo los biocombustibles. Pero algunos productores de mezclas que contemplan la posibilidad de comprar plantas podrían dudar en comprometerse con esos combustibles, ya que en cierto modo no están probados y su disponibilidad podría no ser tan constante como la de las fuentes tradicionales.
Los quemadores de biocombustible de Ammán también pueden utilizar combustibles más tradicionales como el gas natural, el GLP, el petróleo ligero y pesado y el queroseno. Esto alivia las preocupaciones de los clientes que dudan en confiar únicamente en los combustibles más nuevos.

El uso de estos nuevos combustibles es otra victoria significativa en el frente ecológico. Estamos tomando fuentes de energía renovable o, en algunos casos, convirtiendo un producto de desecho en combustible. Esto conserva los recursos naturales y pone menos presión en los vertederos.
En el frente renovable, estamos muy alto en el quemador de polvo de madera. El quemador transforma el polvo de madera, un material disponible de fuentes locales, en un combustible renovable. Lo que hace a este quemador de polvo aún más excepcional es su neutralidad de carbono. El dióxido de carbono liberado al quemar madera se compensa por el hecho de que el árbol consumió esa cantidad de dióxido de carbono durante su vida. Por lo tanto, esta parte de las emisiones es neutra en carbono.
El quemador ha demostrado ser eficaz y se utiliza en varias plantas de mezcla de asfalto de Ammán. También puede ser adaptado a las plantas existentes.
Los biocombustibles, por supuesto, son otra iniciativa. Apoyan la protección del clima y reducen la dependencia del aceite mineral. Ejemplos de estos combustibles son la colza y la caña de azúcar. También se puede utilizar el aceite alto, que es un producto de desecho de la producción de sulfato de celulosa.
Esperamos que en un futuro próximo otros tipos de combustible como el hidrógeno reduzcan significativamente los valores de emisión de gases. Estos combustibles también serán mucho más importantes en nuestra industria. Ammann ya está trabajando en soluciones para estar preparado para esto.
Los dueños de las plantas podrían mirar estos comentarios y decir: "Son grandes ideas, pero ya tengo una planta". ¿Cómo puede un productor de asfalto comenzar a hacer el cambio a una operación más verde mientras utiliza su planta existente?
Los productores de asfalto podrían sorprenderse por lo mucho que pueden lograr con su planta existente. Un primer paso muy fácil es actualizar el sistema de control.
Un sistema de control moderno puede tener un impacto significativo en la eficiencia, y eso afecta a muchas partes del proceso. La mejora de la eficiencia reducirá el uso de combustible, las emisiones y el desperdicio de material. Y el as1 es el mejor en el negocio para hacer exactamente eso.
El entrenamiento es otro paso inmediato que puede ser tomado. La mejor planta y sistema de control del mundo tendrá un rendimiento inferior si el operador no puede aprovechar el valor incorporado.
Otra opción es una adaptación más completa. Sigue costando una fracción del precio de una nueva planta y es compatible con los productos fabricados por Ammann y otros fabricantes.
Un retrofit tiene una gran cantidad de opciones entre las que se puede elegir, incluyendo soluciones de reciclaje. Un retrofit permite el uso de espuma de betún, ceras y otros aditivos. También se puede utilizar betún especial y ciclos de mezcla alternativos.
Una vez más, el propietario de la planta puede determinar el nivel del compromiso. Muchos clientes de retrofit incorporan un nuevo secador, que optimiza la transferencia de calor - y por supuesto reduce las emisiones - y permite el empleo de una amplia gama de materiales, incluyendo RAP.
Una adaptación puede incluir mejoras ambientales para el tanque de betún y el filtro de mangas. También puede incorporar soluciones de reducción de ruido. Se puede hacer una serie de mejoras tecnológicas - incluyendo quemadores renovados, mezcladores y el sistema de control.
¿Cuál es el siguiente paso para un negocio que quiere explorar algunas de las soluciones a las que se refirió?
Deberían ponerse en contacto con los equipos de ventas o de soporte de Ammann. Si no tienen un contacto específico, pueden visitar Ammann.com. Hay un enlace "Encontrar un distribuidor" que aparece de forma prominente en la página de inicio. La página web también tiene una gran cantidad de información sobre todos los productos de Ammann, incluyendo plantas de mezcla de asfalto.