Después de que el viaducto sufriera daños considerables por el gran terremoto de 2001, se planificó su reemplazo.
Los equipos de encofrado de Peri trabajan con una de las mayores tuneladoras de doble escudo del mundo en Seattle.
El viaducto de Alaska construido en los años 50 ha sido considerado una de las vías más importantes a lo largo de la costa de Seattle. Actualmente se está construyendo un reemplazo para el viaducto elevado que se utiliza diariamente por 110.000 vehículos, un túnel de 3,2 kilómetros de largo. Peri planificó y entregó una solución de encofrado específica para la realización de la calzada de dos pisos por la cual la longitud del tubo del túnel previamente perforado se forma en concreto en tres secciones.
Después de que el viaducto sufriera daños considerables por el gran terremoto de 2001, se planificó su reemplazo. Ocho años después, surgieron planes para un túnel tipo BRT. En 2011, Seattle Tunnel Partners (STP) obtuvo el contrato para la planificación y construcción del túnel, una empresa conjunta de Tutor Perini Corporation de California y Dragados USA.
Bertha, una de las tuneladoras de doble escudo más grandes del mundo, realiza un túnel con un diámetro de alrededor de 17,50 m que luego se cubre directamente con segmentos de anillo de concreto prefabricado de 60 cm de grosor. Dentro del tubo, se realiza una calzada de dos pisos. Las paredes requeridas así como la losa de túnel soportada se están formando por medio de soluciones de encofrado móviles de la compañía alemana.
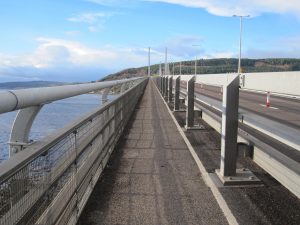
La tarea de los ingenieros de Peri consistía en desarrollar soluciones de encofrado móviles con el fin de obturar y hormigonar eficientemente la construcción de concreto armado dentro del tubo de túnel circular y mover el carro a la siguiente sección. La ejecución se divide en tres fases de construcción, es decir, corbeles, paredes laterales y losas que posteriormente forman la calzada superior. También hay paredes coladas en el lugar por encima de la losa elevada formada con Domino.
Para la planificación, se tuvo que tomar en consideración una amplia gama de condiciones de contorno que incluía las numerosas curvas de túnel así como las inclinaciones laterales requeridas de las losas. Como todos los carros de encofrado de doble escudo están diseñados para ser movidos a lo largo de una misma construcción de carril a través de todo el túnel, la planificación específica de las secciones de hormigonado fue particularmente importante para asegurar una implementación eficiente.
La logística también tuvo que tenerse en cuenta: debido a que suministrar constantemente a la tuneladora con materiales tales como los segmentos de anillo de concreto, el concepto general tenía que incluir un paso suficientemente grande. Los carros de encofrado fueron diseñados para acomodar secciones de 16,45 m de largo, basados en la tasa de perforación promedio esperada de la máquina de perforación de túneles.
Inicialmente, el equipo de construcción niveló el piso del túnel con una capa de concreto sobre la cual se instalaron carriles para mover el carro de encofrado del corbel. Además, se creó una superficie de trabajo plana para la unidad de arranque que constituye la base de toda la construcción.
El primer carro que sigue directamente a la tuneladora lleva el encofrado lateral de la unidad de arranque, un conjunto de encofrado por lado del túnel. El encofrado del corbel era encofrado de acero. La solución Maximo entró después de formar las paredes. Los rieles para los mover la pared y de la losa están en lo alto del corbel.
Por un lado, la unidad de arranque constituye la base para las paredes laterales ascendentes del túnel interior. Por otro lado, también sirve posteriormente como soporte para los paneles prefabricados que se instalan como la losa de la calzada inferior después de que el trabajo de concretado in situ se haya completado finalmente.
Una vez que las cimentaciones han alcanzado la resistencia mínima requerida, las paredes laterales de 4,50 m de altura del túnel interior se forman en concreto directamente. Para ello se utilizan dos juegos de encofrados que consisten en un panel de encofrado Maximo que se traslada de la sección de hormigonado a la sección de hormigonado en un segundo carro de encofrado. Mientras que un conjunto de encofrado permanece en la sección del túnel tras la colocación del concreto, el segundo conjunto de encofrado se vuelve a montar más adelante en el túnel.
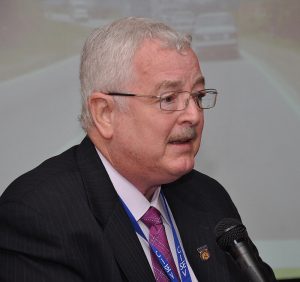
En la tercera fase de construcción, se construye una losa que posteriormente forma la calzada que llevará el tráfico hacia el sur. La losa inferior se realiza con un total de seis carros de encofrado de losa que utilizan el método de la construcción del paso posterior: tres carros levemente más largos con el encofrado específico del proyecto sobre la base de Variokit y vigas del encofrado GT 24 sirven para concretar por adelantado para las secciones de la losa. Los espacios intersticiales resultantes se cierran posteriormente por medio de tres carros de encofrado de losas ligeramente más cortos.