La SP-070 de Brasil también se conoce como la Autopista Ayrton Senna y es una carretera de primer orden en el país, con un tránsito intenso de vehículos. Para su reconstrucción se han sometido a prueba los beneficios en cuanto a ahorro de tiempo, economía y medio ambiente que aporta el proceso de reciclaje en frío.
La SP-070 es una conexión de transporte clave entre São Paulo y Campos do Jordão, Vale do Paraíba y Rio de Janeiro, además de ser la principal ruta de acceso al Aeropuerto Internacional de Guarulhos. Desde 2009 ha sido gestionada por Ecopistas mediante una concesión de 30 años para el mantenimiento de la Autopista Ayrton Senna.
Las máquinas fresadoras pudieron retirar la superficie vieja para convertirla en mezcla mediante su reciclaje.
Se han realizado reparaciones estructurales en una sección de 35 km, el tramo entre los kilómetros 11 y 46, desde São Paulo hacia el este. Estas obras eran urgentes puesto que la base de recorrido con ligazón de cemento de 250 mm debajo del asfalto estaba seriamente dañada debido al gran volumen del tráfico, unos 125.000 vehículos/día en cada dirección, de los cuales el 15% son vehículos pesados de mercancías.
Ecopistas y Fremix Engenharia e Comércio, la compañía contratada para rehabilitar la superficie de la carretera, acordó utilizar una tecnología que aportara buenos resultados en un tiempo breve de construcción. Este material usado reciclado con betún alveolar fue fabricado en la instalación mezcladora móvil de reciclaje en frío de Wirtgen, la KMA 220.
A la hora de seleccionar el mejor método de rehabilitación, los contratistas también tenían que satisfacer una condición esencial: evitar dificultar el flujo del tránsito. En los días laborables, el trabajo de construcción en esta vital ruta de transporte fue restringido a una ventana de 8 horas durante la noche, entre las 9 pm y las 5 am, dado que hasta los cierres más mínimos para realizar obras en la carretera podrían causar embotellamientos masivos del tránsito. El alto volumen del tránsito durante el día no impedía cerrar ningún carril entre el límite de São Paulo y el aeropuerto, por lo que el trabajo tuvo que realizarse durante la noche.
El ajustado plazo eliminó la opción de un pavimento de asfalto grueso (o nueva superficie de concreto). Las capas gruesas de asfalto que se emplean en los procesos convencionales de rehabilitación requieren un tiempo de enfriamiento de unos cuatro días, incluso más para los pavimentos de concreto. La tecnología de reciclaje en frío permitió reparar la superficie de la carretera tramo a tramo antes de abrirse al tráfico inmediatamente. Las ventajas adicionales de este método son la rápida finalización de las obras, un número mínimo de viajes de transporte y el reciclaje del material recuperado.
Las obras de pavimentación fueron realizadas durante la noche para
minimizar las interrupciones del intenso tránsito de la autopista durante el día. El revestimiento de la superficie de asfalto de 100 mm y la subyacente capa estabilizadora de cemento de 250 mm, ambas en necesidad de rehabilitación, fueron fresadas por separado y transportadas a camiones. Para este trabajo, Fremix empleó dos de las grandes máquinas fresadoras de Wirtgen, la W 1900 y la W 200. El material recuperado fue transportado en camión a una ubicación de mezclado en las proximidades de la obra. Fue triturado mediante una trituradora de mandíbulas Kleemann MC 110 Z EVO montada en un camión con el fin de garantizar que el grosor del grano no superara los 20 mm y que el material tuviera una composición granulométrica óptima. Mediante dos instalaciones mezcladoras Wirtgen KMA 220 móviles de reciclaje en frío, el material recuperado fue reciclado para obtener una mezcla de calidad con betún alveolar (BSM). Las dos plantas fueron instaladas rápidamente junto a la autopista, reduciendo así el número de desplazamientos de material. Las máquinas hicieron posible que los empleados del proyecto reutilizaran el material recuperado y que optimizaran el rendimiento añadiendo ligantes y materiales suplementarios, obteniendo un pavimento con una larga vida útil y materiales con buenas propiedades. Loudon International fue responsable del diseño de la mezcla y del control de calidad. En colaboración con los técnicos de JBA Engineering and Consulting, Loudon aportó el apoyo para las investigaciones preliminares y la realización del proyecto. Las pruebas preliminares de los materiales fueron realizadas con la planta de betún alveolar de laboratorio Wirtgen WLB 10 S, en combinación con la mezcladora reglamentaria experimental de doble eje Wirtgen WLM 30. Esto permitió identificar la calidad del betún alveolar y la composición óptima de la mezcla antes de comenzar el trabajo de construcción. La fórmula seleccionada finalmente se compuso de 1% de cal hidratada y 2% de betún.
La KMA 220 permitió procesar los materiales junto a la autopista
El betún caliente se espuma en la cámara de expansión de la KMA 220 añadiendo aire y agua. Así se produce betún alveolar, que es 20 veces el volumen del producto original. El betún alveolar se combina con la cal hidratada y el material recuperado para producir una mezcla homogénea. El material recuperado reciclado fue pavimentado en dos capas: la primera capa de 200 mm de grosor fue compactada mediante una apisonadora de 14 toneladas Hamm 3414 y unos rodillos en tándem Hamm HD 90 de 9 toneladas, y a continuación la HD 90 completó por sí sola la compactación de la segunda capa de 130 mm de grosor. La pavimentadora de orugas Vögele SUPER 1300-3 fue utilizada para aplicar una delgada capa de superficie de 20 mm. Una aplanadora con ruedas de goma Hamm GRW 280 se encargó de la compactación final de la mezcla asfáltica.


minimizar las interrupciones del intenso tránsito de la autopista durante el día. El revestimiento de la superficie de asfalto de 100 mm y la subyacente capa estabilizadora de cemento de 250 mm, ambas en necesidad de rehabilitación, fueron fresadas por separado y transportadas a camiones. Para este trabajo, Fremix empleó dos de las grandes máquinas fresadoras de Wirtgen, la W 1900 y la W 200. El material recuperado fue transportado en camión a una ubicación de mezclado en las proximidades de la obra. Fue triturado mediante una trituradora de mandíbulas Kleemann MC 110 Z EVO montada en un camión con el fin de garantizar que el grosor del grano no superara los 20 mm y que el material tuviera una composición granulométrica óptima. Mediante dos instalaciones mezcladoras Wirtgen KMA 220 móviles de reciclaje en frío, el material recuperado fue reciclado para obtener una mezcla de calidad con betún alveolar (BSM). Las dos plantas fueron instaladas rápidamente junto a la autopista, reduciendo así el número de desplazamientos de material. Las máquinas hicieron posible que los empleados del proyecto reutilizaran el material recuperado y que optimizaran el rendimiento añadiendo ligantes y materiales suplementarios, obteniendo un pavimento con una larga vida útil y materiales con buenas propiedades. Loudon International fue responsable del diseño de la mezcla y del control de calidad. En colaboración con los técnicos de JBA Engineering and Consulting, Loudon aportó el apoyo para las investigaciones preliminares y la realización del proyecto. Las pruebas preliminares de los materiales fueron realizadas con la planta de betún alveolar de laboratorio Wirtgen WLB 10 S, en combinación con la mezcladora reglamentaria experimental de doble eje Wirtgen WLM 30. Esto permitió identificar la calidad del betún alveolar y la composición óptima de la mezcla antes de comenzar el trabajo de construcción. La fórmula seleccionada finalmente se compuso de 1% de cal hidratada y 2% de betún.
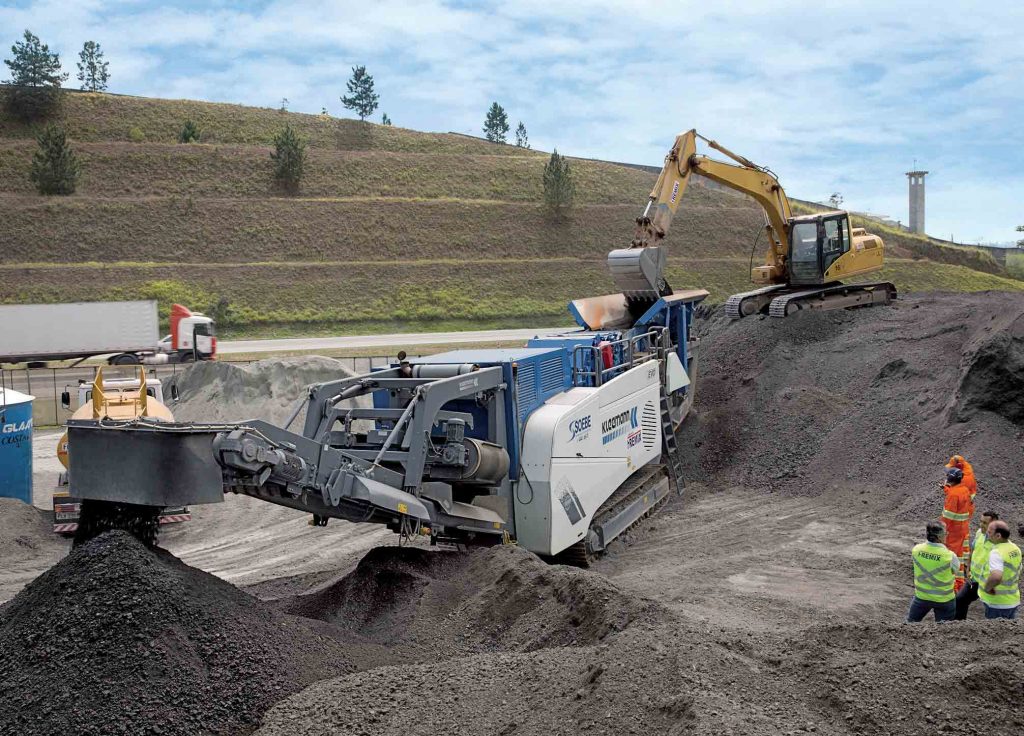