Minimizar el impacto ambiental es una de las preocupaciones latentes de hoy. Los proveedores tecnológicos junto con mandantes y constructores han tomado el desafío en sus manos y hoy se apunta a pavimentos más sustentables.
La industria del cemento ha sido pionera mundial en poner en marcha programas de co-procesamiento de residuos. Actualmente en el mundo se co-procesan más de 10 millones de toneladas de residuos y desechos al año.
Desde hace más de treinta años países como Japón, Estados Unidos, Canadá y miembros de la Unión Europea, han utilizado el co-procesamiento como una alternativa ambientalmente sostenible y económicamente viable en sus procesos productivos.
En América Latina la sustitución de combustibles fósiles ha tomado forma en países como Argentina, Brasil, Chile, Costa Rica, Colombia, Guatemala, México y República Dominicana, entre otros, en rangos que van desde el 7% hasta el 20%. La sustentabilidad también llegó a los pavimentos.
Sacyr ha implementado con éxito el primer pavimento en Chile desarrollado mediante la incorporación de polvo de caucho pretratado (RARx) por vía semihúmeda, proveniente de residuos de neumáticos fuera de uso (NFU).
Esta innovación permite rehabilitar y construir pavimentos en las carreteras con un menor impacto medioambiental, al utilizar mezclas con residuos poliméricos como materia prima provenientes de neumáticos fuera de uso. Con esto, se ha demostrado que por cada kilómetro de carretera que se construye con esta tecnología es posible sacar unos 100 neumáticos aproximadamente de bus o camión desde vertederos.
Para su desarrollo y validación, ha sido necesaria la construcción de diversos tramos de prueba en caminos emplazados en distintas obras de conservación global mixta dentro de la capital chilena, Santiago, como Avenida La Florida y calle Jorge Alessandri, gestionadas por Sacyr. En ambas obras, se han elaborado dos tramos de 1 km cada uno con esta mezcla asfáltica, siendo el segundo país en Latinoamérica -después de México- donde se ha implementado esta tecnología.
Lee también ► Túnel de la Quiebra: Ícono de la ingeniería
La compañía mundial CEMEX anunció en junio pasado una nueva meta más agresiva para estar por debajo de 475 kg de CO2 por tonelada, una reducción de aproximadamente 40% en emisiones de CO2, para 2030.
Además, la firma se comprometió a reducir sus emisiones de CO2 en el negocio de concreto en un 35%, alcanzando 165 Kg de CO2 por metro cúbico, para el 2030. El concreto juega un papel crucial en la industria al ofrecer opciones adicionales más allá del cemento para eliminar el carbono y alcanzar su ambición de neutralidad para 2050.
En la hoja de ruta para alcanzar sus metas 2025 y 2030, CEMEX se basa en procesos operativos existentes, materiales, así como tecnología probada, que ha implementado exitosamente en Europa durante las últimas dos décadas.
Las tecnologías de CEMEX para lograr su nuevo objetivo incluyen el uso de combustibles alternos con alto contenido de biomasa, inyección de hidrógeno, clínker de baja temperatura y bajo CO2, materias primas descarbonatadas, optimización del consumo calorífico de los hornos y la reducción del factor de clínker mediante la mayor adopción de cementos con adiciones en el mercado.
En 2020 el Departamento de Transportes de California (Caltrans), repavimentó una sección de la Carretera 162 en Oroville, usando pavimento asfáltico reciclado y plástico líquido hecho con botellas de plástico de un solo uso, siendo la primera vez que el departamento había pavimentado una carretera usando materiales 100% reciclados. El proyecto piloto cuenta con trabajos en tres pistas de un segmento de 1.000 pies.
La nueva tecnología desarrollada por TechniSoil Industrial de Redding, trata de un tren de reciclaje de equipos que muele las 3 pulgadas superiores del pavimento y luego mezcla las moliendas con un aglutinante de polímero de plástico líquido, que proviene de una gran cantidad de botellas recicladas de un solo uso.
El nuevo material de asfalto se coloca en la superficie superior de la carretera, eliminando la necesidad de camiones para traer material exterior para una operación de pavimentación. Al eliminar la necesidad de transportar asfalto desde el exterior, este proceso puede reducir significativamente las emisiones de gases de efecto invernadero.
Lee también ►Gigantes en Latinoamérica: Plantas de asfalto
Tramo de prueba
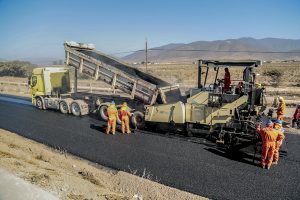
Reducción de CO2
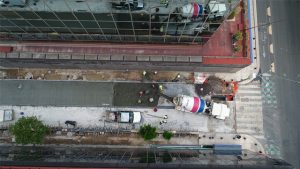
Asfalto con plástico reciclado
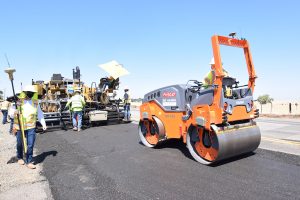