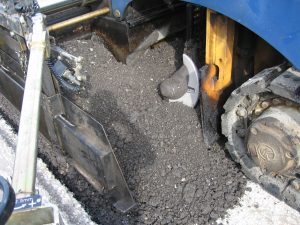
Debido a la creciente demanda de movilidad e infraestructuras viales, teniendo en cuenta también la Economía Circular cada vez más anhelada, el concepto de sostenibilidad ambiental se ha convertido en un elemento fundamental en el campo de la construcción de pavimentos flexibles para carreteras en los últimos veinte años.
La ecosostenibilidad cumple con los requisitos de protección ambiental y dos de sus elementos claves son la reutilización, cuando el material tiene el mismo uso, y el reciclaje, cuando el material se destina a un uso diferente del anterior. Un ejemplo es el conglomerado bituminoso de recuperación utilizable en lugar de agregados vírgenes y betún, que son materiales no renovables. Ampliamente utilizado en todo el mundo hasta 95% para HMA (mezclas asfálticas en caliente) y 100% para CMA (mezclas asfálticas en frio), fresado todavía encuentra dificultades en Italia, donde la bibliografía muestra un uso promedio de 20-30%. Este material aún se subestima porque a menudo se considera erróneamente dañino para la salud y el medio ambiente, porque no siempre se maneja adecuadamente, ya que se considera que limita la vida útil del pavimento y porque las normas técnicas limitan su uso. Teniendo en cuenta la evolución de la ingeniería inherente al estudio de los materiales y las técnicas de producción de los últimos 30 años, llegó el momento de prever el uso correcto del conglomerado bituminoso de recuperación, desde el diseño hasta la construcción de las infraestructuras viales.
1. El conglomerado bituminoso de recuperación
El conglomerado bituminoso de recuperación (también llamado fresado o RAP
- Reclaimed Asphalt Pavement) es el material resultante del fresado o demolición de los pavimentos asfálticos (CB) al final de su vida útil o de los residuos de producción en la planta. Generalmente se compone de agregados, betún y filler unidos entre sí formando así elementos de diferentes tamaños y composiciones (Fig. 2).
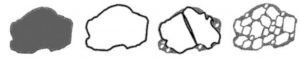
Hasta ahora, en Italia, el conglomerado bituminoso de recuperación fué considerado un desperdicio no peligroso pues no contiene alquitrán de hulla. Recientemente el Decreto 69/2018 ha formalizado que el fresado, si se trata y gestiona adecuadamente, cambia su calificación de "residuo" a "granulado de conglomerado bituminoso". De hecho, el conglomerado bituminoso de recuperación es un elemento fundamental en los procesos de producción de mezclas bituminosas, lo que permite alcanzar los objetivos relacionados con la Ecocompatibilidad y la Economía Circular.
Para obtener pavimentos con CB de recuperación que tengan un adecuado rendimiento y vida útil, el fresado debe tratarse, gestionarse e introducirse en el ciclo de producción de los nuevos CB de acuerdo con las reglas de la técnica y, en cualquier caso, de acuerdo con la legislación vigente.
Para la realización de las nuevas obras, la reutilización del fresado debe preverse desde la fase de diseño y el Reglamento Técnico base de la Licitación debe redactarse de tal forma que contenga todas las pruebas necesarias como garantia de mezclas bituminosas de buen rendimiento: primero (precalificación, diseño de mezcla y posible tramo de prueba), durante (controles de producción) y después (pruebas in situ) de la producción y colocación de las mezclas bituminosas. Las pruebas deben cumplir con las disposiciones de la legislación aplicable vigente (en el país) y garantizar las prestaciones previstas durante la fase de proyecto.
2. La reutilización del Conglomerado Bituminoso de recuperación
Durante varios años, el material fresado se ha reutilizado solo mediante la adición de betún de alta penetración y baja temperatura de ablandamiento, que proporciona la viscosidad final correcta para el procesamiento y la colocación de la mezcla bituminosa. Como alternativa, la tendencia de la última década ha sido agregar aceites derivados de recuperación, que también permiten disminuir la viscosidad del betún envejecido, garantizando así la facilidad de instalación. Sin embargo, ninguna de estas dos soluciones puede implementar los componentes químicos que faltan y, en consecuencia, garantizar el rendimiento adecuado y la vida útil del nuevo pavimento.
Se ha demostrado técnicamente que, incluso en presencia de altos porcentajes de fresado, la adición de Activadores Químicos Funcionales (ACF) permiten, de una parte, garantizar la trabajabilidad correcta y la instalación del conglomerado bituminoso regenerado, asi como, restaurar los componentes químicos que faltan en el betún envejecido contenido en el fresado, asegurando asi un rendimiento y una vida útil adecuados al nuevo pavimento.
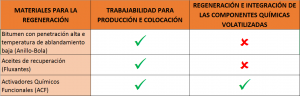
Con el objetivo de demostrar los diferentes comportamientos presatcionales de aceites y regenerantes, a continuación se presentan los resultados de un estudio de laboratorio dedicado..
3. PROGRAMA DE LABORATORIO
Para la comparación del rendimiento, se usaron conglomerados bituminosos de tipo “capa intermedia” según el huso granulométrico de referencia ANAS (ver Gráfico 1).
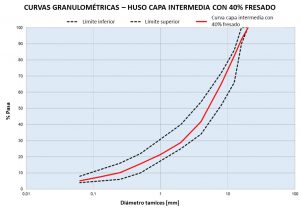
La cantidad de fresado utilizado fue el 40% del peso total de los agregados y, obviamente, se utilizó la curva del fresado post-extracción.
Dada la cantidad de material fresado y la curva granulométrica relativa, que contiene altos porcentajes de de material que pasa el tamiz 2 mm, la proporción utilizada en el análisis no prevee el uso de arena (ver Gráfico 2).
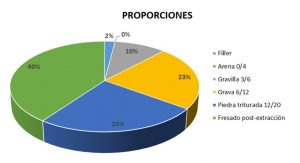
El porcentaje óptimo de betún utilizado es de 4,70% sobre el peso de los agregados, determinado mediante el método de optimización Marshall y calcolado sobre mezcla non aditivada (Véase el Gráfico 3).
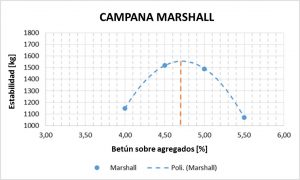
En particular, las mezclas analizadas se reportan en la Tabla 2.
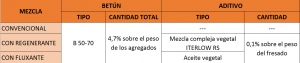
En detalle, el regenerador Iterlow RS utilizado en el análisis es un aditivo específico para la gestión y el uso del fresado reutilizado en caliente. El aditivo se agrega al betún convencional y permite, también, controlar las temperaturas de producción, evitando el aumento excesivo normalmente requerido para el uso de altos porcentajes de fresado.
Por lo tanto, todas las pruebas se llevaron a cabo para la caracterización del rendimiento de las tres mezclas indicadas en la tabla, considerando que algunos parámetros fundamentales para un conglomerado bituminoso son:
- La rigidez y la resistencia a la tracción de los materiales para la correcta distribución de las cargas;
- La falla por fatiga, como consecuencia de la modificación de la estructura interna provocada por las deformaciones repetidas en el material;
- El deslizamiento viscoso con acumulación de deformaciones permanentes bajo la acción de cargas estáticas o dinámicas.
Estos elementos son indicadores de las prestaciones en relación a las grietas y a la formacion de las roderas (ahuellamiento) y, para la relativa determinación, se realizaron los controles reportados en los siguientes párrafos.
3.1 Compactación con prensa giratoria
La compactación de los especímenes utilizados para las comprobaciones del rendimiento se llevó a cabo por medio de una prensa giratoria, de acuerdo con la norma UNI EN 12697-31. La particularidad de este método consiste en ser capaz de ejercer simultáneamente una presión vertical y un movimiento giratorio al especimen. Esta acción reorganiza interna y continuamente sus componentes, adensando las mezclas de una manera similar a lo que se realiza por medio de rodillos. El reprocesamiento apropiado de los datos memorizados por la prensa durante la fase de compactación nos permiten la caracterización volumétrica de las mezclas, la verificación de la trabajabilidad y el grado relativo de adensamiento. Recuerde que una baja compactación coincide con un alto porcentaje de vacíos, con la consecuente reducción en la vida útil del pavimento
3.2 Resistencia a Tracción Indirecta (ITS)
Los especímenes cilíndricos utilizados fueron obtenidos por medio de prensa giratoria y la prueba de resistencia a la tracción indirecta se realizó de acuerdo con la norma UNI EN 12697-23. Consiste en cargar el especímen a lo largo de todo el espesor con una fuerza vertical que desarrolla tensiones de compresión normales en el plano diametral horizontal y tensiones de tracción normales en el plano vertical. La resistencia a la tracción indirecta
a una temperatura dada es la tensión de tracción máxima calculada a partir de la carga máxima aplicada a rotura y de las dimensiones del especímen. Dependiendo de la temperatura y considerando las tensiones-deformaciones generadas en un pavimento al paso de los vehículos, con particular referencia a las capas más superficiales, es evidente que cuanto mayor es la resistencia a la tracción indirecta, mayor es el rendimiento del pavimento.
3.3 Módulo de Rigidez a Tracción Indirecta (ITSM)
Se obtuvieron los especímenes cilíndricos utilizados también por medio de prensa giratoria y el módulo de rigidez se determina según la norma UNI EN 12697-26. La rigidez indica el comportamiento mecánico de los conglomerados bituminosos, la definición de la capacidad de una mezcla para resistir la deformación debido a las tensiones derivadas de la aplicación de una carga, es decir, la capacidad de las diferentes capas para distribuir a la estructura del pavimento la carga ejercida por los neumáticos del vehículo. Se define como el valor absoluto del módulo complejo, representativo de la respuesta de tensión-deformación del material con comportamiento viscoelástico. Dependiendo de la temperatura y la velocidad de aplicación de la carga, el módulo de tracción indirecta se determina usando ensayo dinámico no destructivo. El valor se evalúa como una función de la fuerza vertical aplicada, la deformación diametral horizontal correspondiente y a la relación de Poisson que caracteriza el conglomerado bituminoso. Cuanto mayor es la rigidez, mayor es la capacidad de resistir las deformaciones y la distribución de las cargas.
3.4 Resistencia a la Fatiga
Los especímenes cilíndricos utilizados se obtuvieron por medio de una prensa giratoria y la resistencia a la fatiga se determinó de acuerdo con la norma UNI EN 12697-24. Esta indica, antes la relativa rotura, la capacidad de soportar los ciclos de carga debido al tráfico y las variaciones de temperatura. En particular, el estado de deformación de los conglomerados bituminosos no depende únicamente de la intensidad y el número de ciclos de la fuerza aplicada, sino también de su módulo de rigidez, del gradiente térmico y del procedimiento de compactación utilizado. La prueba se puede realizar en control de la deformación o en control de carga. En el primer caso, la amplitud de la deformación se mantiene constante en la unidad de tiempo y la tensión disminuye debido al fenómeno de fisuración. En el segundo caso, la amplitud de la fuerza se mantiene constante en la unidad de tiempo y la deformación de la muestra aumenta progresivamente hasta que el material se rompe. Se sabe que la elección del método puede influir significativamente en los resultados obtenibles con las mismas mezclas. La elección debe hacerse de acuerdo con la capa analizada y su espesor: generalmente se recomienda, y es más selectivo, el método de control de la deformación, especialmente en presencia de altas rigideces y espesores; para las capas superficiales delgadas, se recomienda el que tiene una deformación controlada. En cuanto al módulo de rigidez, la verificación de la resistencia a la fatiga debe realizarse tanto a altas como a bajas temperaturas. De hecho, para las mezclas bituminosas a medida que aumenta la temperatura, el componente elástico aumenta y la viscosa disminuye, con el consiguiente aumento de la resistencia de la muestra. Cuanto mayor sea la resistencia a la fatiga, mayor será la vida útil del piso.
3.5 Creep Dinámico
El Dynamic Creep es una prueba de compresión cíclica determinada de acuerdo con la norma UNI EN 12697-25 y permite identificar las deformaciones permanentes con respecto a los ciclos de carga impuestos. De hecho, la muestra cilíndrica se carga con una tensión constante a 40 °C durante 3600 impulsos. Los resultados de la prueba de Creep que caracteriza a un conglomerado bituminoso son:
- el valor de la deformación permanente (raramente se encuentran en el campo internacional valores de limites críticos, pero se llevan a cabo pruebas comparativas);
- la pendiente de la curva debe ser lo más baja posible porque, con las mismas deformaciones permanentes, indica mayores tiempos de acumulación.
El valor de la deformación permanente depende de la mezcla en sí, de la carga, de la frecuencia, del número de ciclos y de la temperatura. Es evidente que, bajo las mismas condiciones, las mezclas con menor deformación y menor pendiente de la curva son las que garantizan pavimentos con mayor rendimiento.
4. RESULTADOS
Los análisis a continuación se refieren a muestras producidas con una prensa giratoria de acuerdo con los siguientes parámetros:
- Presión vertical = 600 ± 3 kPa;
- Ángulo de rotación = 1,25° ± 0,02;
- Velocidad de rotación = 30 giri/min.
4.1 Compactación
Considerando un contenido de vacíos óptimo del 3%, que para la mezcla en cuestión corresponde a una densidad media igual a 2.410 kg /dm
3, la primera verificación consistió en determinar el número de ciclos de prensa giratoria necesarios para alcanzar este grado de compactación . Como se muestra en los Gráficos 4 y 5, observando que el número de ciclos de la prensa correspondientes a la compactación in situ para una capa intermedia no reciclada con betún convencional, es igual a aproximadamente 100 ÷ 120, está claro que el número de ciclos necesarios para obtener la compactación correcta para la mezcla:
- CONVENCIONAL es en promedio aproximadamente 190, demostrando dificultad de trabajabilidad, sobretodo en el caso de operaciones manuales;
- REGENERANTE es en promedio aproximadamente 140, indicando una buena trabajabilidad y garantizando una compactación correcta;
- FLUXANTE es en promedio aproximadamente 80, lo que revela una trabajabilidad demasiado alta relacionada con la posibilidad de deformar el pavimento en lugar de compactar la mezcla bituminosa adecuadamente.
4.2 ITS
Como se ve en la Tabla 3, la verificación del ITS muestra que para las mezclas:
- CONVENCIONAL y REGENERANTE la resistencia es en promedio igual a 1,64 MPa;
- REGENERANTE el coeficiente de tracción indirecta es inferior, en promedio, del 13% respecto al de la mezcla CONVENCIONAL, indicando una rigidez menor de la mezcla;
- FLUXANTE la resistencia es en promedio inferior del 36% respecto al REGENERANTE
- FLUXANTE el coeficiente de tracción indirecta es en promedio inferior del 30% respecto al CONVENCIONAL, indicando una reduccion significativa de la rigidez de la mezcla.
4.3 ITSM
Las pruebas se llevaron a cabo siguiendo las siguientes configuraciones:
- Frequencia = 2 Hz;
- Rise-time = 124±4 ms;
- Coeficiente de Poisson = 0,35.
Como se puede ver en la Tabla 4, la verificación ITSM muestra que los módulos de rigidez para las mezclas:
- CONVENCIONAL en promedio son más altos a todas las temperaturas;
- REGENERANTE son en promedio más bajos que el CONVENCIONAL de aprox. 5%, 12% e 26%, respectivamente a 5°C, 25°C e 40°C;
- FLUXANTE son en promedio más bajos que el CONVENCIONAL de aprox. 17%, 16% e 14%, respectivamente a 5°C, 25°C e 40°C.
Es evidente que tanto el regenerante como el fluxante permiten reducir la rigidez del pavimento que contiene el fresado, como se indica en la Tabla 1.
4.4 Resistencia a Fatiga
Las pruebas se realizaron siguiendo las siguientes configuraciones:
- Temperatura = 25°C;
- Rise-time = 0,40 s;
- Control de deformación = 100 me;
- Coeficiente de Poisson = 0,35.
Como se muestra en el Gráfico 6, la verificación a fatiga muestra que, respecto al CONVENCIONAL, los ciclos de carga para el FLUXANTE aumentan y que el efecto es aún más evidente para la mezcla RIGENERANTE.
Por ejemplo, a 50 me de deformación, respecto al CONVENCIONAL, se tiene que los ciclos de carga de la mezcla:
- FLUXANTE son 5 veces superiores (de 10.000 a 50.000);
- RIGENERANTE son 10 veces superiores (de 10.000 a 100.000).
4.5 Creep Dinámico
Las pruebas de Creep Dinámico son el objetivo futuro de este estudio. Incluso si actualmente ya los resultados muestran comportamientos totalmente diferentes entre un regenerante y un aceite fluxante, esta prueba verificará el diferente nivel de deformaciones permanentes que ocurrirán durante la vida útil del pavimento, o sea el relativo ahuellamiento.
5. CONCLUSIONES
Los análisis llevados a cabo compararon tres tecnologías diferentes de reutilización del fresado:
- CONVENCIONAL solo con la adición de betún de primer uso;
- FLUXANTE con la adición de aceites vegetales fluxantes;
- REGENERANTE con la adición de una mezcla compleja vegetal con una fórmula especifica para la regeneración de betunes envejecidos (Iterlow RS).
Los resultados han demostrado que para evaluar el rendimiento de una mezcla que contiene fresado, es esencial llevar a cabo una serie de pruebas:
- Compactación;
- Tracción indirecta;
- Módulo de Rigidez;
- Resistencia a Fatiga;
- Creep Diná
Osea, la simple verificación de una sola de las prestaciones reportadas no es suficiente. En efecto, para poder ser identificada como una mezcla con buenas prestaciones, esta debe garantizar contemporáneamente ser adecuada en:
- trabajabilidad durante la fase de puesta en obra, para obtener el contenido correcto de vacíos;
- resistencia a la tracción indirecta, para evitar la formación de grietas y su propagación;
- rigidez para asegurar la distribución de cargas;
- resistencia a los ciclos de carga para garantizar la vida útil del pavimento.
Por lo tanto, es suficiente que solo una de las características de rendimiento no se cumpla para reducir el ciclo de vida del pavimento y aumentar la probabilidad de deterioro a corto plazo.
Los resultados obtenidos muestran cómo el uso de un agente regenerador correcto (mezcla REGENERANTE) permite aumentar la vida útil del pavimento sea respecto al uso del betún en la mezcla (mezcla CONVENCIONAL) como al uso de fluxantes (mezcla FLUXANTE). Sin embargo, para las mismas mezclas, las pruebas de Creep ya están siendo evaluadas, lo que resaltará cualquier problema relacionado con el ahuellamiento debido al betún fluxado.
Por lo tanto, como ya se destacó en la primera parte de este documento que para un contenido de fresado de más del 10%, es necesario utilizar aditivos que permitan regenerar el betún envejecido presente en el material de recuperación.
Por lo tanto, con el objetivo de realizar estructuras de pavimentos viales eco-sostenibles y satisfacer la Economía Circular para pavimentos realizados siguiendo a la perfección las técnicas necesarias y que poseen una alta vida útil, los proyectistas deben considerar la reutilización del material fresado desde las primeras etapas, imponer la regeneración relativa y elaborar los estándares técnicos adecuados. que imponen la ejecución de los controles de las mezclas durante la producción y colocación.