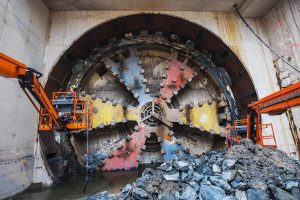
Foto:Frank Jansen
La construcción de un nuevo proyecto de túnel en Holanda está a cargo de BAM Infra, que cumple con las estrictas restricciones ambientales establecidas por el Gobierno de los Países Bajos. El proyecto Rotterdamsebaan, como se le conoce, implica la construcción de la nueva carretera para la Ciudad de La Haya, que incluye la construcción del túnel.
El proyecto para construir esta nueva conexión de carretera y túnel es necesario para hacer frente a la congestión de tráfico pesado en el área. En la actualidad, los vehículos que viajan hacia y desde La Haya dependen de una serie de rutas, una de las cuales es la Utrechtsebaan (A12) que transporta alrededor del 40% del tráfico que entra y sale de la ciudad y ha sufrido una congestión severa, particularmente en los períodos pico. La congestión del tráfico también afecta áreas residenciales como Rijswijk y Voorburg en La Haya, así como las áreas circundantes.
Sin embargo, abrir el enlace Rotterdamsebaan, que mide alrededor de 4 km en total, ayudará a abordar el problema del tráfico. Hará que La Haya y el área que la rodea sean más accesibles según los socios del proyecto.
Rotterdamsebaan conectará las autopistas A4 y A13, así como la carretera de circunvalación central de la ciudad. Transcurre desde el intercambio de Ypenburg, entrando en un corte en la zona de Vlietzone y luego va bajo tierra cerca del aparcamiento en Drievliet. La sección subterránea de Rotterdamsebaan corre bajo Westvlietweg, Voorburg-West, el sitio arqueológico Forum Hadriani y el puerto de Binckhorst. El camino vuelve a emerger en Binckhorst por Zonweg, donde se une con Binckhorstlaan y Mercuriusweg. El túnel ha sido diseñado para que los vehículos viajen a velocidades de hasta 70 km/h.
BAM Infra está construyendo el proyecto vial Rotterdamsebaan a un costo de unos US$340 millones. El enlace incluirá dos rampas de 450m de largo, 650m de corte y cubierta de túnel y las secciones de doble túnel que se han aburrido con la ayuda de un TBM masivo.
Una mejora clave será la reducción de vehículos pesados que usan carreteras secundarias en el área. En general, la apertura del tramo de la carretera y el túnel ayudará a distribuir el tráfico de vehículos de manera más uniforme, al tiempo que reduce los movimientos de vehículos en carreteras menores, así como para el Utrechtsebaan existente (y sobrecargado). Para los conductores, el problema de congestión se reducirá significativamente y los tiempos de viaje serán más cortos. Desde una perspectiva de seguridad, una mejor distribución del tráfico de vehículos al nuevo túnel reducirá los riesgos para los usuarios vulnerables de la carretera, como los ciclistas y peatones a lo largo de las carreteras secundarias.
En construcción
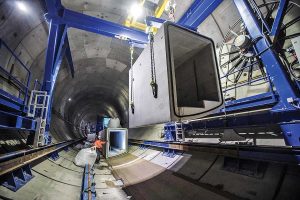
Foto: Frank Jansen
El proceso de licitación transcurrió de 2014 a 2015, con BAM Infra ganando el acuerdo y comenzando su trabajo preparatorio en 2015. Se utilizaron técnicas convencionales de movimiento de tierras para eliminar el material de las secciones de la rampa y los tramos de túnel de corte y cubierta.
Las secciones del túnel perforado se condujeron utilizando una máquina perforadora de túneles (TBM) construida por el especialista alemán
Herrenknecht. Para el proyecto, la TBM se llamó Catherina-Amalia.
La máquina estaba equipada con un escudo mixto con un diámetro de 11,34 m, que impulsaba los dos tubos gemelos de 1,6 km de largo en un período de 12 meses. Sin embargo, el trabajo fue complicado, entre los cuales se debió al hecho de que el área del sitio estaba abarrotada y que el equipo tenía que garantizar que el flujo de tráfico continuara durante la construcción.
Los socios del proyecto, sin embargo, tenían experiencia en las condiciones, ya que habían realizado previamente trabajos de tunelado en el área entre 2013 y 2015. La misma TBM se había utilizado para conducir el túnel Sluiskil entre Goes y Gante, que se abrió al tráfico en mayo de 2015. Este enlace también presenta tubos gemelos y mide alrededor de 1,6 km de longitud, mientras que fue construido para reducir los problemas de congestión sobre el puente Sluiskil existente. Después de que el TBM llevó a cabo el trabajo del Túnel Sluiskil, la máquina fue devuelta a la planta de Herrenknecht en Kehl, Alemania, para ser restaurada y preparada para su próximo contrato.
El trabajo para conducir el primer agujero del túnel Victory Boogie Woogie se llevó a cabo entre enero y julio de 2018. Con un peso de 1.600 toneladas y una longitud de 80 m, la tunelera TBM tuvo que desmontarse y colocarse en posición para la segunda unidad. Aunque complejo, este proceso se llevó a cabo dentro del cronograma y la TBM pudo perforar el segundo tubo, comenzando con esta parte del trabajo en septiembre de 2018. La TBM utilizada fue nombrada para el trabajo y terminó su segunda unidad el día 10 de enero de 2019 para completar su trabajo para el túnel Victory Boogie Woogie.
En total, la TBM de 80m de largo excavó más de 330,872m3 de material y en el punto más profundo, los túneles están a 31m bajo tierra. Conduciendo el túnel Victory Boogie Woogie, la TBM demostró ser altamente productiva y Herrenknecht dijo que la máquina fue capaz de alcanzar tasas de avance de hasta 30 m/día en un punto durante su segunda conducción.
Al igual que con el Túnel Sluiskil, las condiciones del terreno para el Túnel Victory Boogie Woogie resultaron difíciles, con arena, limo y arcilla propensa a obstrucciones.
Sin embargo, la experiencia previa con el túnel Sluiskill significaba que la TBM se podía configurar específicamente para hacer frente a las condiciones. Estaba equipada con una cara de corte abierta, con transporte directo de material desde el centro, así como un circuito de lechada especialmente adaptado.
Una vez que se condujo el enlace del tubo gemelo, los lados del Túnel de Victoria Boogie Woogie se apoyaron utilizando segmentos prefabricados. Uno de los túneles tiene 818 secciones de anillo completas, mientras que el otro tiene 820 secciones de anillo. Cada anillo en sí está compuesto por ocho componentes, por lo que el túnel más largo presenta 6.650 de estas unidades prefabricadas, mientras que el otro túnel tiene 6.544 de los componentes. Cuando el trabajo de revestimiento se completó, permitió que se construyera la plataforma con dos carriles en cada tubo. Además, se construyeron conexiones de túnel cruzado a intervalos de 250 m para unir los tubos gemelos, con el objetivo de aumentar la seguridad y proporcionar acceso de mantenimiento.
La carretera para ambos túneles se ha construido sobre un lecho de concreto con una superficie de asfalto que permite un espacio libre de altura máxima de 4,7 m.
Ruta limpia
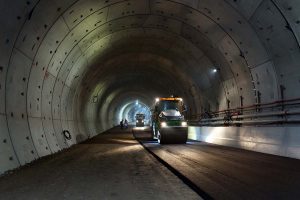
El proyecto ha tenido que cumplir con los estrictos requisitos medioambientales y, por este motivo, se están utilizando una serie de soluciones sostenibles para el túnel. El impacto del trabajo para construir el proyecto se ha reducido al minimizar los movimientos del tráfico de construcción, así como al construir un enlace de carretera temporal.
Se ha tenido en cuenta el impacto visual del portal en Vlietzone, con su diseño destinado a "encajar con el paisaje verde de la zona".
Las soluciones medioambientales incluyen la instalación de paneles solares que proporcionan toda la energía eléctrica necesaria para la sala de control del túnel. Se utiliza iluminación LED de baja energía, lo que reduce la potencia requerida y también minimiza la necesidad de mantenimiento a largo plazo, dada la longevidad de las unidades. Los sistemas también incluyen reducción de polvo fino (FDRS) que utiliza filtros instalados en los portales del túnel para optimizar la calidad del aire dentro del enlace. Los constructores de túneles han instalado el FDRS para abordar el problema de las partículas dentro del túnel.
Mientras tanto, las superficies de las carreteras están utilizando un asfalto de grado LEAB especial que presenta el uso de RAP. Las bombas también se instalan dentro del túnel para eliminar el agua de lluvia, y esto se pasa al sistema de alcantarillado local para su eliminación segura.
Otras medidas de sostenibilidad utilizadas durante el proceso de construcción han incluido el uso de calidades de combustible más limpias en el sitio y la instalación de equipos de difracción de sonido para minimizar la transmisión del ruido del tráfico.
Elevación pesada
Un gran desafío para el proyecto llegó en la forma de la enorme TBM. Debido a la gran escala de TBM, Sarens, un especialista en levantamiento y desplazamiento, fue contratado para mover la máquina. Este fue un papel clave para toda la operación de perforación de túneles y
Sarens llevó a cabo el trabajo en nombre de su cliente Combinatie Rotterdamsebaan.
Junto con
Herrenknecht, la empresa se encargó del transporte inicial y el montaje del TBM al sitio de construcción. La empresa necesitaba transportar la TBM en 50 secciones separadas desde la fábrica de Herrenknecht en Alemania hasta el sitio en los Países Bajos, con la pieza más pesada que pesaba unas 130 toneladas y medía 5,7 m de ancho por 4,4 m de alto.
Cuando llegaron los componentes, el equipo comenzó a ensamblar la TBM y la grúa sobre orugas necesaria para el levantamiento inicial. Sin embargo, el espacio disponible para la operación de la grúa era limitado, por lo que Sarens optó por usar su grúa LR1350-1 por su capacidad y capacidad de maniobra en espacios reducidos.
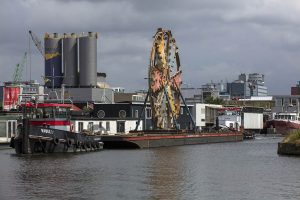
Debido al área de trabajo restringida, algunas partes de la tuneladora tuvieron que ensamblarse primero cerca del eje de lanzamiento y luego transportarse utilizando transportadores móviles autopropulsados (SPMT) a la grúa sobre orugas para el elevador. La tripulación también utilizó una segunda grúa móvil para la instalación del remolque de respaldo.
Utilizando un equipo de 10 miembros a la vez, Sarens llevó a cabo los elevadores para el cabezal de corte, el cilindro de acero de 120 toneladas y la estación de bombeo de 70 toneladas, que requirieron dos grúas móviles que funcionaban en conjunto.
Sarens también tuvo que transportar los componentes de laTBM de vuelta al eje de lanzamiento después de haber sido utilizado para conducir el primer orificio. Después de que la TBM llevó a cabo la perforación del segundo túnel, Sarens volvió a desmontar la máquina y la transportó fuera del sitio.
Sin embargo, la segunda fase del proyecto en particular, para mover la TBM nuevamente al eje de lanzamiento después de que el primer túnel se había aburrido, no estuvo exento de desafíos.
Uno de estos desafíos fue que la última parte de la TBM que se desmontó también fue la primera parte necesaria para el reensamblaje. Para asegurarse de que el trabajo de reensamblado no afectara el cronograma del proyecto, el equipo de Sarens tuvo que planificar toda la operación de transferencia con cuidado para asegurarse de que cada tarea específica se programara correctamente.
El tamaño real de la TBM fue en sí un desafío. Si bien la mayoría de los componentes de la TBM eran de un tamaño que significaba que podían moverse por carretera, seis eran simplemente demasiado grandes y pesadospara esta opción. En cambio, estas secciones tuvieron que transferirse utilizando un SPMT y una barcaza.
El SPMT grande presentaba no menos de 24 ejes, mientras que la barcaza medía 45 m de largo por 7 m a través de la viga. Sarens también usó una serie de otros equipos grandes para mover los componentes de TBM. Estos incluían una grúa sobre orugas LR1350-1 con capacidad de 350 toneladas, una grúa todoterreno AC700 con capacidad de 700 toneladas y dos grúas móviles: una LTM1400-7.1 y una LTM1130-5.1.
El escudo de corte de la TBM presentaba un diámetro de 11,8 m y su tamaño significaba que era simplemente demasiado ancho para moverse a lo largo de las carreteras o sobre puentes en el área. Como resultado, Sarens estableció un sistema de soporte que permitiría levantar el escudo verticalmente. Luego, el personal usó el sistema de soporte para levantar el escudo de corte en una sola pieza, primero para transferirlo desde los SPMT a la barcaza, y luego desde la barcaza, de regreso a los SPMT.
La barcaza tuvo que hacer tres viajes a lo largo del canal para mover los componentes más grandes. Fue atracado al lado de donde se encontraba una grúa con una capacidad de 700 toneladas en una vía pública. Luego, la grúa transfirió piezas desde la barcaza a los SPMT para su posterior transporte.